Here at Meyer, the rapid spread of COVID-19 has caused us to reevaluate how we approach senior living design, and what it might mean to design for a world that will never be quite the same, especially in senior living communities across the country. The coronavirus pandemic has unleashed fundamental change throughout the world as everyone comes to terms with this new, unprecedented reality. As design professionals, Meyer’s Senior Living Studio has researched and explored how design will change and affect senior living communities in the immediate future and in the long term. Readiness Design is awareness, applications and tools for senior living developers, operators and owners to consider in order to combat the spread of COVID-19 or other potential outbreaks while maintaining a safer and healthier community.
Building Systems
It is likely that new mechanical codes will play a large role in dictating what measures developers and operators will need to take in future developments. ASHRAE has already mobilized a taskforce to look at all building classifications and system design in a post pandemic world. Some of these measures can be implemented now. Here are a few of the more practical ones that may not significantly impact construction costs:
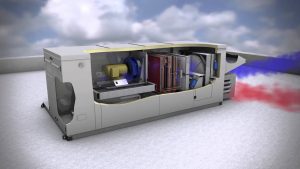
- Increasing airflow particularly from outside air. This will promote cleaner air and cycle out older air more quickly. A Dedicated Outdoor Air System (DOAS) can provide 100% outdoor air to common areas utilizing more ductwork and using VAV boxes to maintain minimum ventilation amounts.
- More robust filtration system in mechanical units. Merv 13 filtration systems, an anti-microbial filter which captures a higher percentage of particulate matter, can be provided in units that serve common spaces such as restrooms and dining spaces. This could result in more energy consumption. Another step includes a more aggressive maintenance program to change out filters on a shortened replacement schedule.
- Higher humidity levels greater than 40% can inactivate most viruses in a short amount of time. Consider adjusting your humidity levels with your HVAC system.
- Mandatory anti-microbial coatings within ductwork. Consumers and businesses alike are looking for innovative and effective ways to address odor causing bacteria, mold and mildew. Anti-microbial coatings and protected clean surface technology is leading the way by design.
- Air purifiers not only clean existing air but can increase air changes when the existing HVAC systems are unable to increase airflow. Portable air purification units are cost effective and easier to locate around a facility, however, air purification units can also be permanently installed in the ceiling and switched on and off as needed.
- Far-UVC light: As mentioned in Insight 2: Technology, specifically designed ultraviolet (UV) technology can sanitize and eliminate up to 99.9% of germs, bacteria, and viruses by modifying and destroying their genetic material (DNA/RNA) preventing further replication. UV lamps in direct recessed lights, downlights or even in ductwork can kill microorganisms within the airstream. A more cost effective solution would be to install UV germicidal sterilization right at the source of outside air introduced into the building. Future codes may require UV lamps on resident unit HVAC equipment.
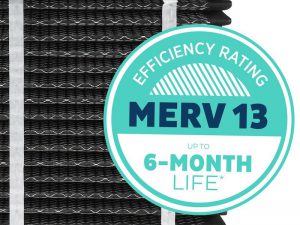
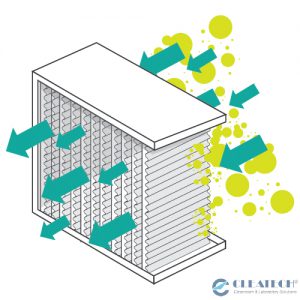
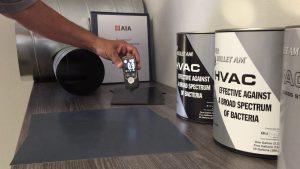